Multi-gas detector are protect workers in a variety of environments, including enclosed spaces like manholes, sewers, and other areas with poor ventilation. They detect gases like oxygen (O2 Monitor), hydrogen sulfide (H2S Monitor), carbon monoxide (CO Monitor), and lower explosive levels (LEL Monitor) of a variety of combustible gases. We offer a range of monitors for you to choose from. View our gas monitor choices below. You can also get a reliable single-gas H2S monitor, O2 monitor, CO monitor.
Which gas can a multi-gas detector detect?
Multi gas detectors, which include 4-gas detectors, are detect the amount of various harmful gases in the air as well as the supply of oxygen to make sure workers can breathe safely on the job. These devices can be used to detect a range of harmful substances. The most common of which include:
Carbon Monoxide:
CO is an odorless, colorless gas that can be fatal in large quantities. It is most often found in the exhaust fumes of combustion vehicles, including cars, trucks, and other industrial equipment. It can also come from stoves, grills, generators, and furnaces. Prolonged exposure or exposure to large quantities can result in a variety of symptoms, including dizziness, fatigue, nausea, vomiting, and chest pain. In severe cases, it can lead to fainting and even death.
Hydrogen Sulfide:
H2S is a colorless gas that often smells like rotten eggs, which is why it’s often referred to as sewer gas. Though your sense of smell is extremely unreliable as an indicator of concentration. It is common in the wastewater, natural gas, and oil refining industries. It is heavier than air, which causes it to sink to low-lying areas. Exposure to H2S can lead to nausea, headaches, confusion, fainting, and even death.
Oxygen:
Most 4-gas monitors will also monitor the level of oxygen in the atmosphere. Every worker needs access to oxygen to breathe. Monitoring oxygen levels can help prevent injury and death on the job. The Occupational Safety and Health Administration (OSHA) mandates that all oxygen gas detection instruments trigger an alarm when oxygen level drops below 19.5% volume.
These monitors can also be used to detect a range of harmful substances and gases that may be present in the workplace, such as:
Methane:
Methane is considered relatively nontoxic but high levels will reduce the amount of oxygen in the air, which makes it difficult to breathe, especially if the person has a respiratory condition such as asthma. This gas is also extremely flammable, which often poses a bigger risk.
Irritant Gases:
Some monitors may measure the levels of irritant gases, usually ammonia or chlorine, that can cause respiratory issues such as bronchitis or bronchiolitis. When these fumes are inhaled, they can cause an inflammatory reaction in the respiratory tract. These gases are heavier than air, so they also sink to the bottom of the atmosphere.
Choose a multi-gas monitor based on your specific needs and the risks of the job at hand.
What LELs does multi-gas detector read?
Aside from multi-gas detector assessing the presence of main gasses which include oxygen, carbon monoxide, hydrogen sulfide, they also detect lower explosive levels (LELs) of flammable, combustible gasses. LELs are the lowest concentration of a gas or vapor in air that can combust if an ignition source like a flame or heat is present. Some monitors also read the upper explosive limit (UEL), which is the maximum level a gas needs to ignite. Every gas comes with its own LEL and UEL based on how much is in the air. The monitor reads the amount of gas based on how much is needed for it to ignite, usually expressed as %Vol.
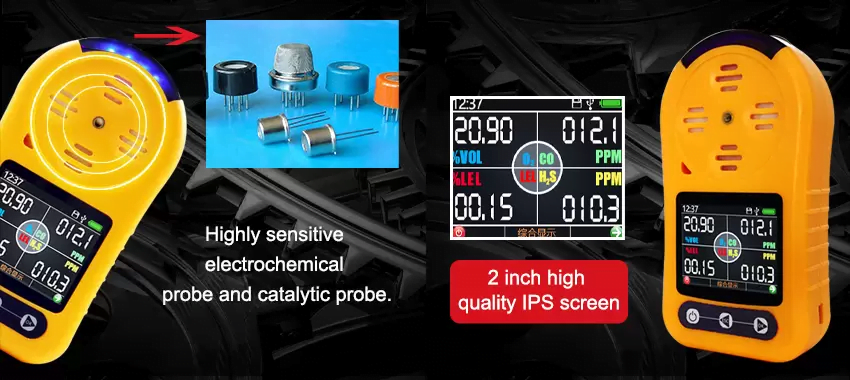
A reading of 0% Volume means there is no gas detect in the air. A reading of 100% means the gas has reached its LEL. For example, methane comes with an LEL of 5%. If the monitor detects methane that makes up 2.5% of the overall atmosphere, the meter reads as 50% LEL, which means the gas is halfway to reaching its lower explosive limit.
Understanding these LEL gas readings is crucial when it comes to preventing injury and death on the job. Workers need to know when it’s safe to use equipment in the workplace, including those with an ignition source. This equipment would otherwise combust if exposed to flammable gasses.
Knowing the LEL of these gasses also relates to your health. OSHA has set clear standards when monitoring gasses in the workplace. Every hazardous gas has a permissible LEL. Once the gas passes this threshold, it may start to cause health problems.
How does a four gas monitor work?
There are lots of different gas monitors to choose from. These devices use different types of sensors to detect the levels of the target gases in the air.
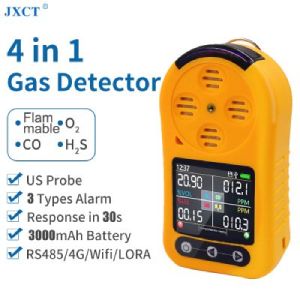
Many devices use electrochemical sensors to detect hazardous gases, especially hydrogen sulfide. The gas will trigger an electrochemical reaction when exposed to the sensor, which creates a small electric signal in the monitor. This signal produces the readings on the monitor.
Most 4 in 1 gas detector use catalytic sensors to detect various types of gases. The device has a platinum-coated wire inside that will start to oxidize when exposed to combustible gases, including carbon monoxide and methane. This sets off the alarm when high levels of gases are present.
Both types of multi-gas meters will issue an alarm when the gas has surpassed a certain threshold, usually the permissible LEL. Other teams will lower the threshold, especially when working in unpredictable settings, to give them more time to evacuate in an emergency.
The alarm may be audible, visible, or physical (vibration), depending on the make and model. It’s often best to use a monitor that produces all three, so the person can feel, see, and hear the alarm. This is especially important when working in noisy areas or those with poor visibility.
Once the alarm goes off, workers should evacuate the area immediately. They may need additional safety equipment to continue working in the space, such as face masks and respirators. Another option is to ventilate the space and retest the area before going back inside.
Many teams will store their multi-gas detectors in a docking station when they aren’t in use. The station will automatically charge the device and recalibrate the sensors to ensure the readings are accurate. Workers can then pick up the device the next day without having to perform these tasks manually. The station will also perform a bump test by exposing the sensors to a known quantity of a target gas to test if it works properly. It will recalibrate the device if the readings don’t match the known quantity accurately.
Workers should also inspect their gas monitors at the start of every shift. They should check for dust and dirt that may clog the sensor. We store our equipment in a dry, room temperature location to maximize its working life.
Other teams will use fixed gas monitors that remain in the same location day after day. This is often the best choice when working in the same environment, such as an office, garage, or workroom. The monitor stays connected to a power source for continuous monitoring.